How the Baking Industry Is Molded by Injection Molding Machines
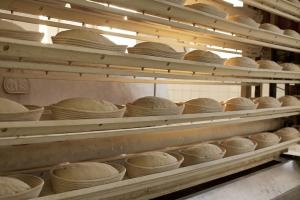
Without a doubt, the plastics industry forms a significant part of the market both internationally and on a local level, especially amongst bakeries.
With this strong foothold in the world economy, it’s reasonable to expect manufacturing protocols be as efficient as possible to meet such extreme demands.
Second to extrusion by a small margin, injection molding is the predominant manufacturing technique for handling polymers and is estimated to be responsible for producing 32% of all plastics.
For facilities that manufacture products from thermoplastic materials, much like the polypropylene baking racks at D&V Plastics, injection molding machinery is invaluable for all things plastic processing.
How Do Injection Molding Machines Work?
The functionality of all injection molding machines can be broken down into three central elements:
- Injection unit/Plasticator – the molten plastic is prepared and transferred through the injection unit at high pressures into the mold.
- Mold – in most instances, molds are precision machined from steel or aluminium by a toolmaker which allows the molten plastic to conform to the geometric features of the final product. For ease of extraction of the solidified plastic melt, molds are designed to be separable by way of a parting line.
- Clamping – tasked with keeping the mold firmly in position, opening and closing it, as well as discharging the finished product.
The practical nature of the injection molding process comes to life when accounting for its versatility, which also owes to its prevalence. These machines allow facilities plenty of headroom to manufacture products for bakeries, such as baking racks, that are simple or intricate, and small or large, all within precise tolerances.
On top of this, bakeries partner with bakery suppliers that are in possession of such machinery as this headroom allows for handling custom requests without lengthy production times. For instance, D&V Plastics has the logistical pipelines in place to produce 60 custom baking racks per hour in compliance with clients’ specifications.
Much of our efficiency rides on the back of our investment into housing two Nissei FVX660 Hybrid Injection Molding machines. Which brings us to…
What Is a Hybrid Injection Molding Machine?
Naming conventions for injection molding machines are determined from the type of injection unit/plasticator that is used. The three main driving systems that help classify injection molding machines are as follows:
- Hydraulic – oil pressure in this system provides the capital needed for plasticisation, injection into the mold cavity, closing the clamp, holding the clamp, releasing the clamp, and finally ejecting the molded product.
- Electrical – much of the environmental concerns are addressed through use of these machines, but they require higher upfront costs. A combination of servo and main-spindle drives are responsible for powering the injection molding process.
- Hybrid – taking the best of both hydraulic and electrical systems, injection molding machines of this calibre strike a delicate price-performance balance. On account of this, bakeries and bakery suppliers are reaping the rewards due to the servo motors allowing for faster cycles, tighter tolerances, and consistent quality for the manufacture of baking racks.